Swapfiets has the ambitious goal of a 100% circular product by 2025. To achieve this, we have to take an in-depth look at every aspect of our product. The good news is: our circular business model helps us with this goal. Thanks to the fact we retain ownership over our products, we are supplied with a high volume of data. This gives us great insights to create a future-proof product.
An example of how we use this data is for our lights system. Previously, we had battery-powered lights, and our data showed that this was the cause of many repairs. So we redesigned these, and now they have no batteries or need for cable management, leading to a drastic reduction in repairs needed. This design has already changed the game for us, but the ride does not stop here. It is in our nature to continue striving for a fully circular product. As such, there are still areas to improve this part.
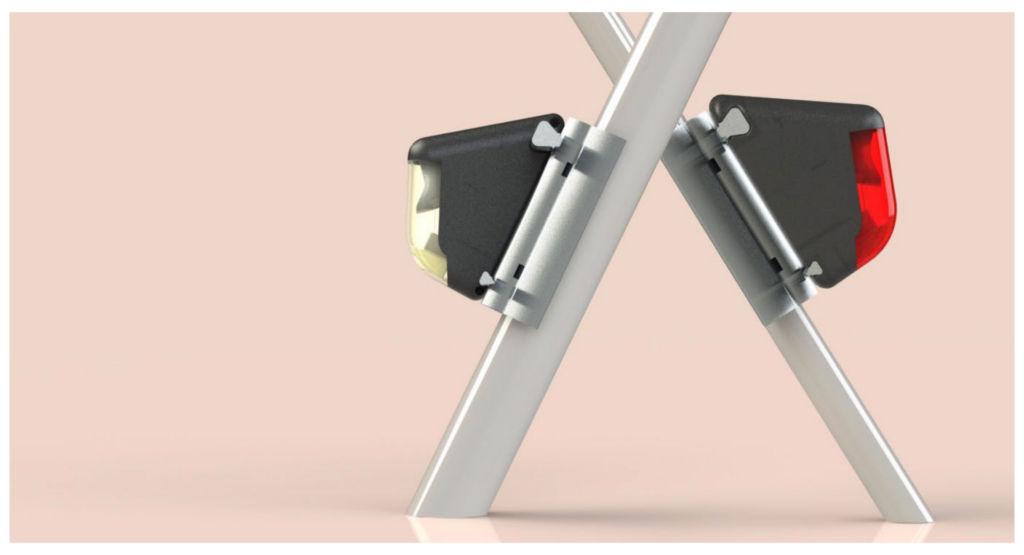
So we challenged 20 Product Design students from Hogeschool van Amsterdam to redesign our light, and we asked them to consider these 4 circular principles throughout their process:
- Designed to last & easy to repair
- Made out of renewable content
- Zero pollution anywhere in the entire life cycle
- Zero waste
Lots of innovative ideas came out of this challenge. We have interviewed the winning team – Studio Naadloos – to share insights into their approach and perspectives with you.
Studio Naadloos is made up of Wikki van Leijden, Thom Schrama and Julius Kroot, their winning design – Rebate – can be seen above.
Can you tell us about the project, what was the aim of what you were trying to achieve?
The aim given was to create a circular bicycle lighting system for Swapfiets. To help them achieve their goal to be 100% circular product by 2025. Our main focus was on the repairability of the lights, to make sure that all components can be separated from each other, so the lighting can be recycled or reused and most importantly be easily repaired. In order to extend the life expectancy of the part.
Wikki
So, how did you decide to approach this problem?
In the beginning we were all a bit stuck with the idea of creating a bicycle light because actually there are already a couple of pretty good options out there, and also the lighting system that you are using right now to reelight is pretty epic in its concept. The only downside of it is that you can’t take it apart, so it’s just a big piece of electronic waste. At some point we realised, maybe then we shouldn’t try to reinvent the wheel, but let’s just focus on the issue that we’re facing here and try to see if we can come up with the same sort of system but make it just really easy to repair.
Thom
Can you tell me a little more about your final design?
We came up with our design Rebate. This contributes to circularity by its repairability. All components can be separated from one another and be replaced when necessary. Another unique thing about our design is the breadboard principle that we integrated, so the LEDs can be easily replaced when they are broken. LEDs are the components that are the ones that break first, so it’s important that these can be changed, to improve the total cost of ownership.
Wikki
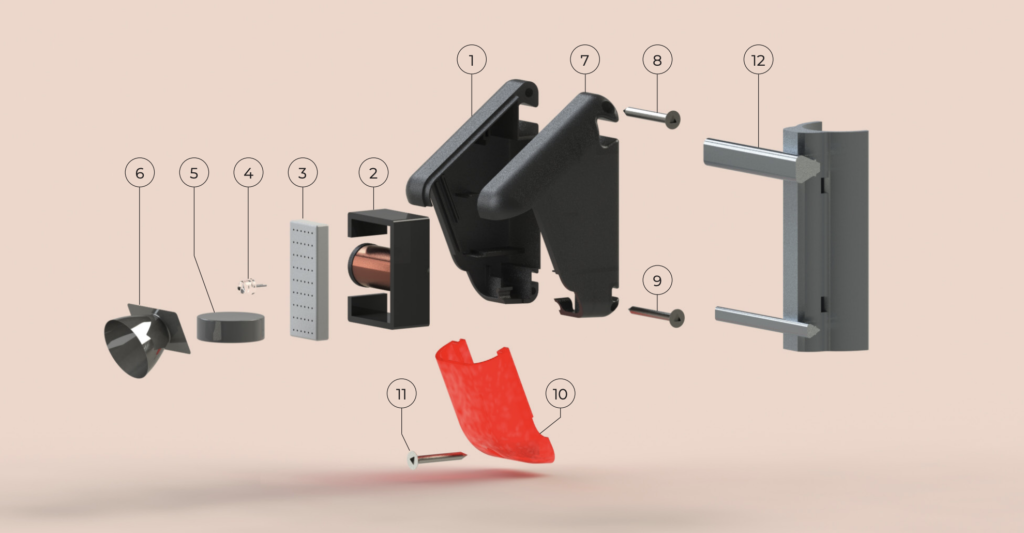

How easy is it to do these repairs, is a special skill set required?
We tried to make it as easy as possible, a big part of this project was to bring down the total cost of ownership, and one of these things is to be very quick in the repairs. So if you want to use a principle which is relying on replacement, everybody is supposed to be able to do it. Especially if there’s a new guy on the job, who needs to install a new light on the breadboard, he needs to be able to do it on his first intuition guess. Pop it open, plug the replacement in and move around again.
Julius
The Relight is ultrasonically sealed (how they seal the plastics on top of each other), but that means that you can’t open it without breaking it. So we tried to come up with a way where we could close off our components in a housing so that if water would enter, there would not be a problem. Instead of trying to keep the problem out, we said OK let’s just accept that it might happen and then see how we can work with it. So we made it away for water to go within the housing and then to disappear through the bottom again. Because water always takes the easiest route, we just gave it that route.
Thom
How did you go about choosing the specific materials of the components?
Well we looked at in the beginning at the very broad scope of what the materials were available and what would work in the production method that you are going for. But in the end a lot of these things come down to it the question – is it recyclable? We can work with a very nice bioplastic but then you won’t be able to recycle it, because there’s no system in place. So we actually in the end came up with trying to use a plastic that is already used by Swapfiets in a lot of different places already. So we actually make the amount of materials in a Swapfiets smaller, and by doing that we make the waste flow of the same kind of plastics bigger.
That’s the beauty of working for a client like this, as all the materials go back to Swapfiets. We could make the light out of gold and still we would get it back, so we could be a bit more free with the material choices.
Another thing that we thought was really cool, is the cone that reflects the light, and makes it stronger. The problem with that, is that you need something that is very reflective. You need to chrome a certain material. And chroming is a horrible thing anyway, and you are also blending different materials together – which is never a good idea. I called with a couple people who are doing a lot of sustainable design, and asked them “what is a good alternative for this thing”. And they came up with the idea of using old soda cans for the reflector cone. Which is a waste product already, and then we found a way to reshape them into the product that we needed.
Thom
To what extent did you consider the environmental footprint when the sourcing suppliers?
We did do a comparison between producing our own parts in China or locally in the Netherlands. And the funny thing is that it is only a tiny bit more expensive to produce them here. But the footprint is so much less. As the designers we say go for local production with a low footprint, instead of having to import it in bulk and having the impact.
Thom
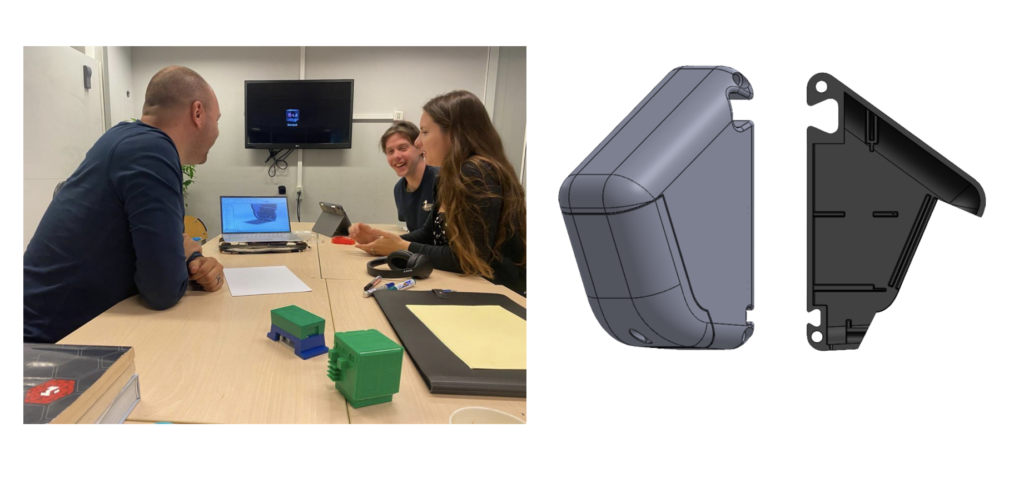
What were your main takeaways from working on this project?
My main takeaway was that circularity is more complex that I thought in the beginning. You have to think about the whole system. And all choices you make have advantages and disadvantages. Which was quite hard during the project. There were many stakeholders to consider, with the Earth and users being the main ones. But to satisfy them fully was quite the challenge.
Wikki
What are your suggested next steps, where should Swapfiets go from here?
We think it’s a very noble goal to be 100% circular by 2025. After doing this project I’m really seeing how hard it is to accomplish this goal. Because we have been putting our three brains to it for the past 20 weeks, to work out how to get this light more and more circular. I suggest hiring different students or experts on these projects. It’s really nice to get new input from fresh young teams. Who are really willing to work on it.
Julius
The work all these students have done has provided us at Swapfiets with new insights into approaches that we can take to make our products more sustainable. Here’s to a more circular future!